Resistant Cables for Drinking, Waste and Hot Water Systems
Resistant Cables for Drinking, Waste and Hot Water Systems
1. Introduction
“Water is Life!” After oxygen, the most important element in human life is water; because life begins with water. Throughout history, civilizations have been established near water. In addition, many methods have been developed for the transportation, preservation, and use of water, as well as for protection from water-related disasters. After the industrial revolution, electricity, along with water, has played a significant role in the formation of modern civilization. The most important way to reduce the damage caused by global climate change and greenhouse effects to our atmosphere is to produce electricity from clean, renewable, and sustainable energy sources. Hydroelectric power plants and renewable energy sources (such as solar and wind power) are among the most well-known environmentally friendly and compatible energy sources. In this article, we will discuss the characteristics of water-resistant cables, the tests applied to them, and how they are used in integrated systems. For cities, towns, villages, or even the simplest settlements to be livable, and for industries and organized industrial zones to be operational, it is necessary to safely transfer drinking or wastewater or other critical liquids (such as oil, gasoline, etc.) from one place to another using submersible pumps with high IP protection class. In systems to be established for the transfer of drinking water, wastewater, or hot water, the materials to be used must meet certain standards to protect the quality of the water, prevent damage to the system, especially cables, or ensure that the system can continue to operate for a long time.
2. Usage Areas of Water-Resistant Cables
When we look at the usage areas of water-resistant cables, many different sectoral usage areas emerge. Generally, we can divide cables working in water into two main classes: • Use in drinking water • Use in wastewater Thanks to the diverse product range within Prysmian Cable, we offer many solutions for wet areas as well as on land. Our water-resistant cable solutions are designed for immersion or submersion in different usage conditions, ranging from 300/500 V to 18/30 kV voltage levels, from 1.5 m to 2000 m, or from 40°C to 120°C.
- Immersion: To dip or submerge an object partially into a liquid.
- Submersion: To completely immerse or submerge an object into a liquid.
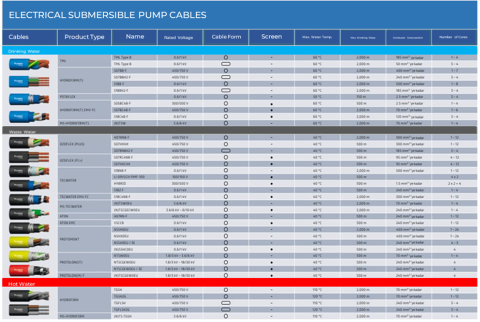
Cables used in wastewater need to have outer sheaths that are resistant to abrasive environments such as oil or chemical compounds and have high mechanical strength, as they are used in systems belonging to treatment plants or industries. On the other hand, the outer sheaths of cables to be used in drinking water must not release any chemicals or components into the water or degrade the quality of the water in any way. Cables to be used in this context should be evaluated under the “Drinking Water Directive.” You would like to reach the details about the topic with the below link; https://www.resmigazete.gov.tr/eskiler/2005/02/20050217-3.htm
3. Europe Unioun Drinking Water Directives (2000/60/EC)
This directive aims to protect human health by specifying the health and purity requirements that must be met in drinking water. It covers all waters intended for human consumption, except for natural mineral waters and waters that are considered medicinal products.
According to the directive:
- It does not contain any microorganisms, parasites, or other substances that pose a potential risk to human health.
- It specifies the parameters for minimum requirements related to microbiological, chemical, and radioactivity aspects.
- It mandates the necessary measures to ensure the health and purity of water intended for human consumption.
4. Approving Water-Resistant Cables
Many countries have rules, regulations, and tests implemented through their local administrations.
For instances;
- Water Regulation Advisory Scheme (WRAS) – United Kingdom
- Elastomerleitlinie of Umwelt Bundesamt (ELL) – Germany
- Kunststoffer und Trinkwasser (KTW) – Germany
- Attestation de Conformité Sanitaire (ACS) – France
- Regulation on Water Intended for Human Consumption – Turkey
Generally, their purpose is to “regulate the procedures and principles related to the compliance of water intended for human consumption with technical and hygienic conditions, ensuring water quality standards, extraction, packaging, labeling, sale, and inspection of spring and drinking waters.” However, regarding the waterproofing of materials to be used in liquid-contact environments, especially water, the International Protection Code – IP system, determined according to the IEC 60529 or EN 60529 standard published by CENELEC (European Committee for Electromechanical Standardization) and accepted worldwide, is used.
The standard classifies the degrees of protection provided against the ingress of solid objects (including body parts such as hands and fingers), dust, accidental contact, and water/moisture. The IP code consists of 2 digits and optionally 2 extra letters. The first digit (0, 1, …6 or X) defines the protection against the ingress of solid foreign objects and access to hazardous parts, while the second digit (0, 1, …8 or X) defines the protection against the ingress of water.
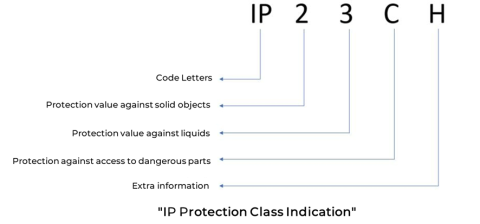
Since cables have a closed structure due to layers such as insulation, filling, and outer sheath, it is not entirely accurate to talk about the IP protection class. Instead, it would be more appropriate to refer to the protection against water (Against Water - AW). Water-resistant cables are generally produced to correspond to level 7 (Immersion*) or level 8 (Submersion**) in the protection class against liquids. They should be selected according to the technical specifications to be applied based on the environmental conditions in which the cable will be used.
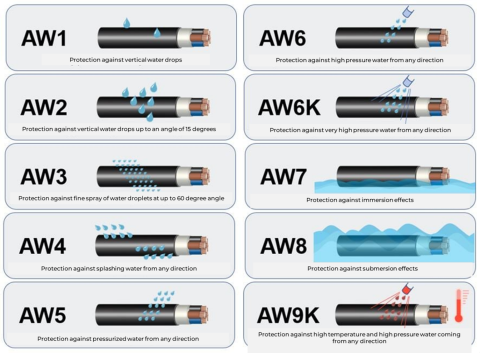
“Display of Protection Class Against Liquids Under the International Protection Code (IP)”
At the core of water-resistant cables are the “H07RN-F” series products with rubber-based insulation and outer sheath, thus adhering to the “TS EN 50525-2-21” standard. According to this standard, “H07RN-F” type cables are approved for use in “dry” and “damp and wet” (AW7–Immersion) areas but do not provide the feature of complete submersion in water (AW8–Submersion). Prysmian’s OZOFLEX-H07RN-F type cables can be given as an example of this. For the submersion feature, i.e., continuous underwater working conditions, the “H07RN8-F” type cable stands out in the TS EN 50525-2-21 standard. Prysmian’s “OZOFLEX PLUS” series products can be given as an example of this cable type.
We can divide the cables in this category into two main groups based on insulation material.
These are:
- Thermoplastic - Polyvinyl Chloride (PVC)
- Cross-linked compound Elastomers Ethylene Propylene Rubber (EPR)
- Ethylene Vinyl Acetate (EVA)
- Silicone Rubber (SIR)
Generally, Thermoplastic or Elastomeric compounds are preferred for inner or outer sheath materials.
The main ones are:
- Chlorosulfonated Polyethylene (CSP)
- Polychloroprene (PCP)
- Chlorinated Polyethylene (CPE)
- Silicone (SR)
- Ethylene Propylene Rubber (EPR)
- Polyurethane (PU)
Each insulation or sheath material is selected or specially combined according to its unique properties. While silicone and EVA compounds allow for higher operating temperatures and consequently higher current capacities, EPR has excellent dielectric properties, flexibility at low temperatures, and resistance to ozone-ionization and various weather conditions. For example, Ethylene Propylene Rubber (EPR) is produced by combining it with additives to achieve waterproofing and marketed under the brand “HYDROFIRM,” while Polychloroprene (PCP) is combined with additives for high mechanical strength and abrasion resistance and marketed under the brand “CORDAFLEX.”
On the other hand, elastomer-insulated cables are made from insulation and inner/outer sheath compounds that provide excellent performance in extreme ambient temperatures. Generally, the maximum allowable operating temperature based on the conductor is 90°C, while the maximum short-circuit temperature is 250°C. Meanwhile, the minimum allowable temperatures during operational activities (installation, transportation, and storage, etc.) can drop to -25°C / -40°C.
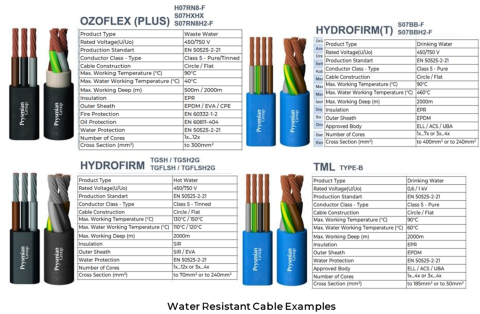
5. Electrical Tests
Electrical tests consist of a total of 4 stages, including pre-tests and subsequent tests. In the first stage, a sample of at least 20 meters is taken from the product to be tested and immersed in drinking water at 20°C (±5°C) for at least one hour. Then, an alternating current voltage test is applied according to TS EN 50395 Clause 6. During the test, there should be no puncture in the insulation. After the pre-test, in the second stage, a 5-meter piece is taken from the 20-meter sample and subjected to a 1 kV alternating current test while immersed in drinking water at 50°C (±2°C) for 100 days. There should be no power interruption or short circuit during the test period. After the pre-voltage tests, for the third stage, three core samples, each 5 meters long, are taken from the first 20-meter sample that passed the test. These are immersed in drinking water at 50°C (±2°C) for at least 24 hours and then subjected to a 2.5 kV alternating current test between the conductor of each core and the water for 5 minutes. There should be no power interruption or short circuit during the test period. Immediately after this test, the insulation resistance should be measured at 50°C (±2°C) according to TS EN 50395 Clause 8.1. In the final and fourth stage of electrical tests, the three tested samples are subjected to a 1 kV alternating current test while immersed in drinking water at 50°C (±2°C) for 14 days. There should be no power interruption or short circuit during the test period. Immediately after this test, the insulation resistance should be measured again at 50°C (±2°C) according to TS EN 50395 Clause 8.1. 5.2. Mechanical Tests Mechanical tests must be applied to all layers of the cable, regardless of the inner or outer sheath, according to the structure of the cable. From each layer of the cable sheath or sheaths, a total of 12 samples are taken, consisting of 4 sets of 3 spoon/dumbbell samples each, as explained in TS EN 60811-501 4.2.3 b). These samples are exposed to 20°C (±5°C) and 50% (±5) relative humidity for 7 days.
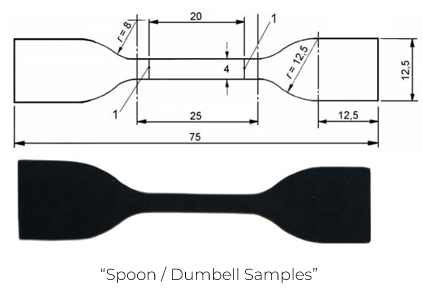
In the first stage, one of the sets is weighed to 0.1 mg for weight measurement and then kept in drinking water at 50°C (±2°C) for 100 days. In the second stage, the samples in this set are exposed to 20°C (±5°C) and 50% (±5) relative humidity for 16 hours, then reweighed to check if they still weigh 0.1 mg. For mass increase, tensile strength, and elongation at break tests, the other 3 sets are subjected to the following conditions:
- Without exposure to any liquid.
- Immersed in drinking water at 50°C (±2°C) for 28 days.
- Immersed in drinking water at 50°C (±2°C) for 100 days.
To determine if there is any mass increase, the mass of the sample exposed to water for 100 days should be at most 40% of its mass before exposure to water. For tensile strength and elongation at break, the samples kept in water for 28 days and 100 days should meet the minimum values specified in TS EN 50525-2-21 Table E.1, and the variation rates should be within the specified values.
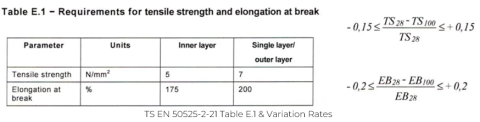
You can access details about our water-resistant cable products via the Water Treatment | Prysmian Group link. Water-resistant cables can be produced and used based on the TS EN 50525-2-21 standard according to their areas of use, or they can be used together with or as substitutes for cables produced for different sector solutions. Among these are the “PROTOMONT™” or “PROTOLON™” branded mining cables. These cables are designed to withstand the harsh conditions of the mining sector. Protection against water and oil is among these features.
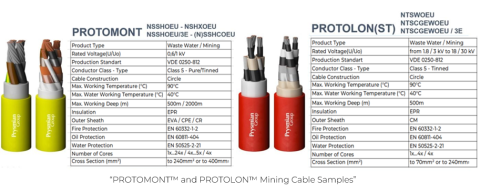
In cases where protection against water is required as part of special operating conditions, certain other product groups, such as fiber optic, copper communication, and high-voltage cables, can also be applied based on the suitability of production standards. Cables are often exposed to harsh environmental conditions, including UV radiation, humidity, temperature fluctuations, wind, snow, and rain. Consequently, cables are among the first components to indicate system faults. Moreover, they can cause power outages and may not be limited to cable replacement alone; they can also damage other components, leading to high repair and replacement costs.
Selecting products and components is critical in any electrical system. High-quality cables of appropriate gauge, along with optimized safety measures, contribute to longer-lasting systems. Conversely, subpar or low-quality cables can quickly deteriorate, reducing the system’s electrical production capacity and, consequently, its revenue. Each kilowatt (kW) lost due to poor-quality cables represents a significant investment loss.
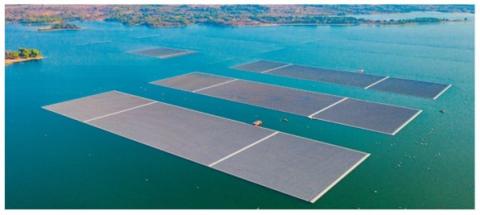
Solar (photovoltaic) cables (H1Z2Z2-K) used in energy production serve as an example of integrated systems. As the world’s energy demand continues to rise, there is a growing shift toward sustainable and renewable resources such as wind and solar energy. Prysmian Group assists renewable energy enterprises worldwide in turning this opportunity into reality. With a constant awareness of our responsibility to the planet, we collaborate with stakeholders in the renewable sector, supporting projects that benefit both our world and businesses. Our commitment to innovation remains steadfast in the industry.
To bring the electricity generated from solar power plants (GES) located on water to the mainland, you need waterproof cables that can withstand challenging environmental conditions. Our comprehensive knowledge of special operating conditions allows us to offer solutions to both submersible pumps and important manufacturers in the photovoltaic industry. Our complete, high-performance, and reliable product range ensures long service life and suitability for wet environments.
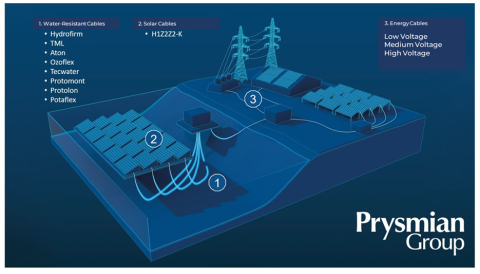
6. Conclusion
As Prysmian Kablo, we offer a wide range of suitable and high-quality cables for both land-based and marine needs. For instance, whether you’re harnessing solar energy from panels anywhere or distributing it through power grids to homes and offices, our cable solutions have you covered. Our technologies, which include cables used in photovoltaic (GES) installations on land, rooftops, or water, provide comprehensive cable solutions for contractors, developers, grid operators, transmission and distribution system operators, and panel manufacturers. Our extensive cable portfolio encompasses low-voltage, medium-voltage, and high-voltage cables, as well as specialized cables for communication and control, all in line with current standards.